Double Acting Fork Pneumatic Actuator
Bidirectional Operation
High Efficiency
Durability
Ease of Maintenance
Safety
Cost-Effectiveness
Adaptability
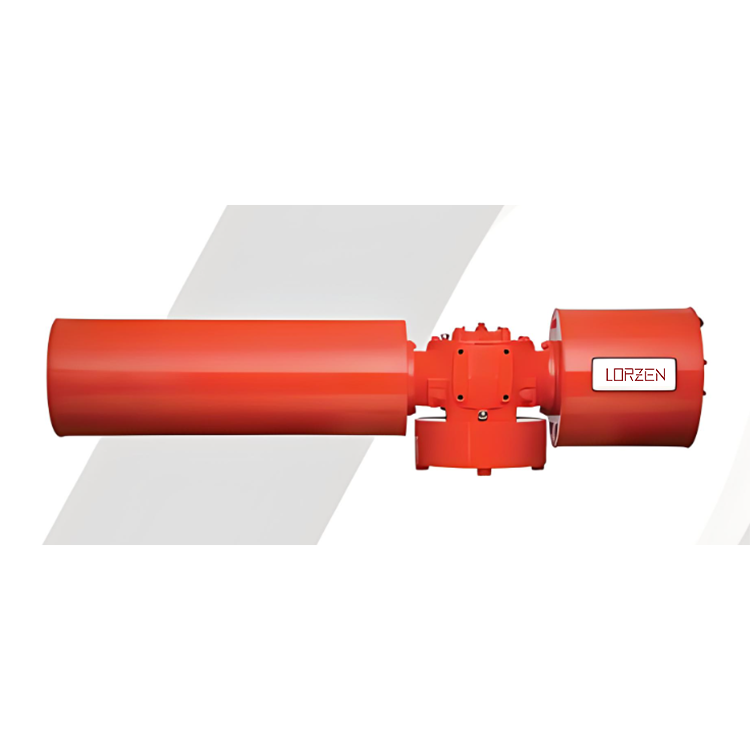
Double Acting Fork Pneumatic Actuator Gallery
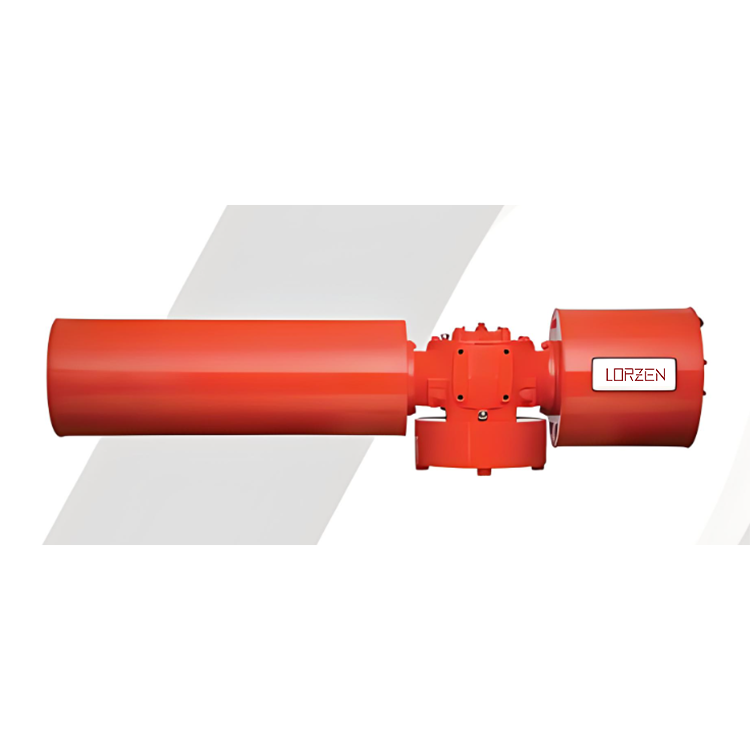
Double Acting Fork Pneumatic Actuator
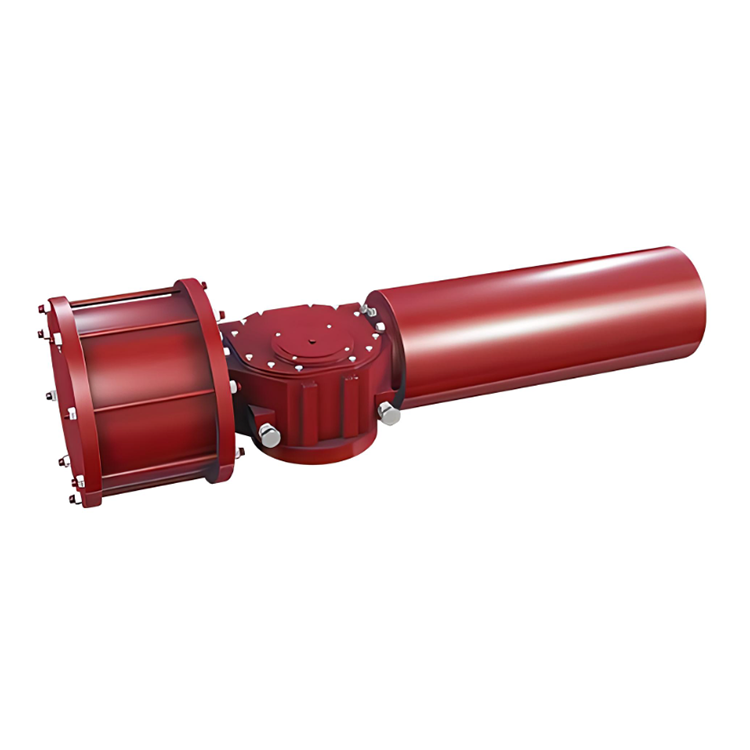
Double Acting Fork Pneumatic Actuator
Every LORZEN Double Acting Fork Pneumatic Actuator has gone through highly controlled conditions to ensure the high quality of your Pneumatic Actuators.
Technical features:
Double Acting Fork Pneumatic Actuators have a number of advantages that make them widely used in various industrial applications. Here are some of the main advantages:
Bidirectional Operation: The bidirectional operation means that the actuator can provide precise control in two directions (usually open and close), which increases its flexibility in various applications.
High Efficiency: Double Acting Fork Pneumatic Actuators are capable of generating a large amount of force in a short period of time, making them perform excellently in applications where quick response and high force are required.
Durability: Due to their robust construction and high-quality materials, these actuators are typically very durable, capable of operating for long periods under various harsh environmental conditions.
Ease of Maintenance: The design of the Double Acting Fork Pneumatic Actuator makes maintenance relatively simple, typically requiring only regular inspections and replacement of worn parts.
Safety: Due to their operating principle, Double Acting Fork Pneumatic Actuators typically automatically close or open to a preset safe position in the event of a loss of power or air supply, increasing their safety in hazardous environments.
Cost-Effectiveness: Although the initial cost of Double Acting Fork Pneumatic Actuators may be higher, their high efficiency, durability, and low maintenance requirements typically provide good cost-effectiveness in the long run.
Adaptability: Thanks to their simple design and operating principle, Double Acting Fork Pneumatic Actuators can adapt to a variety of different applications and environments, including high-temperature, high-pressure, and corrosive environments.
Product characteristics:
Double Acting Fork Pneumatic Actuators are actuators that utilize compressed air to provide power and force to mechanical systems. Their double-acting capability means they can control mechanical motion in two directions, which is typically achieved by using compressed air to drive a piston within a cylinder that can be directed to move in any direction.
The term “fork” in the name refers to a specific mechanical design characteristic. In fork-style actuators, the piston rod is connected to the output shaft through a fork, allowing the actuator to convert linear motion into rotational motion. This design is particularly useful in applications that require control over devices that need to perform rotational movements, such as valves.
Pneumatic actuators use the power of compressed air to generate motion. This makes them suitable for applications where electricity is impractical or hazardous. They are also commonly used in applications that require clean, dry power, as air can be filtered and dried to prevent contamination.
Double Acting Fork Pneumatic Actuators are used in a variety of industrial applications, including manufacturing processes, energy systems, chemical plants, water treatment facilities, and food and beverage production lines. They are typically used to automate the operation of valves, doors, dampers, and other mechanical systems that require precise control.
Performance characteristics:
The product features of Double Acting Fork Pneumatic Actuators may vary depending on the specific manufacturer and model, but the following are some typical key features:
Bidirectional Operation: Ability to operate in two directions, which usually means it can switch between opening and closing.
High Force Output: These actuators are typically capable of generating high force output, making them suitable for applications that require a large amount of force.
Fast Response: The actuator is designed to respond quickly to inputs, which is crucial for applications that require a quick reaction.
Durability and Reliability: Actuators are usually made from high-quality materials, allowing them to operate over long periods under various environmental conditions.
Simple Maintenance: The design of the actuator makes maintenance and replacement of parts relatively simple.
Automatic Safety Position: In the event of a loss of power or air supply, the actuator typically automatically closes or opens to a preset safe position.
Environmental Adaptability: The actuator is designed to work under various environmental conditions, including high temperature, high pressure, and corrosive environments.
Multiple Interface Options: Actuators typically offer multiple interface options to interface with various control systems.
Optional Manual Operation: Many models offer a manual operation option to manually control the actuator when required.
Configurable Action Range: The action range of the actuator can be configured to suit specific application needs.
Please note that these features may vary depending on the specific product model and manufacturer, so when choosing an actuator, these features should be evaluated based on your specific needs and applications.
Operating Parameters:
Rotation angle:0°~90°
Output torque
Double action:600~260000Nm
Spring restoration: 600~100000Nm
Operating pressure
Pneumatic drive:0.3~0.7Mpa
Hydraulic drive:20Mpa
Operating temperature
Standard -20℃~+80℃
High temperature -15℃~+150℃
Low temperature -40℃~+80℃
Performance Testing
Our state-of-the-art facilities allow rigorous testing to validate function, endurance and environmental protection.
Quality Assurance
100% testing and inspection ensures superior performance of every actuator.
LORZEN Pneumatic Actuators Are Utilized Across Various Sectors, Including:





Actuator Design
Double Acting Fork Pneumatic Actuator Search
Pneumatic control system is an important part of any valve and actuator. has rich experience in gas circuit control to meet clients’requirements for on-off, regulating and urgent switching-off. Gas circuit system can be installed on a panel or in control cabinet, or in-stalled on an actuator or placed separately.
- +8613736966003
- sales@lorzval.com
- Lorzen Factory Park, Linyang Industrial District, Oubei Town, Yongjia County, Wenzhou City, Zhejiang Province, China
Double Acting Fork Pneumatic Actuator Related Information
Installation and Maintenance
Installation and Maintenance
The installation and maintenance of a Fork Pneumatic Actuator are relatively straightforward. Here are some basic steps:
Installation: During the installation process, it’s important to ensure the actuator is correctly aligned and secured in the right position. The actuator should be properly interfaced with the driven device (such as a valve or other mechanical component) to ensure accurate and efficient operation.
Maintenance: Maintenance of the actuator typically involves regular inspections and replacement of worn parts. This might include replacing seals, cleaning and lubricating moving parts, and checking and adjusting the control system. In most cases, just carrying out these maintenance steps periodically can ensure long-term reliable operation of the actuator.
Industry Applications/Functional Uses
Industry Applications/Functional Uses
Fork Pneumatic Actuators have a wide range of uses in many different industries and applications. Here are some of the main application areas:
Manufacturing: On automated production lines, these actuators can be used to control a variety of mechanical equipment such as valves, drums, conveyors, etc.
Energy Sector: In the oil, gas, and electricity industries, these actuators can be used to control various types of valves, ensuring efficient distribution and use of energy.
Chemical Industry: In chemical processes, these actuators can be used to precisely control conditions for various chemical reactions, such as temperature, pressure, and flow rate.
Water Treatment: In water treatment facilities, these actuators can be used to control various equipment like pumps, valves, and filters, ensuring effective water treatment.
Food and Beverage Industry: In the production process of food and beverages, these actuators can be used to control various equipment like mixers, ovens, and packaging machines, ensuring efficiency and quality in the production process.
These are just some of the main application areas for Single Acting Fork Pneumatic Actuators. Thanks to their simple design and operating principle, these actuators can adapt to a variety of different applications and environments.