120°-180° Stroke Pneumatic Actuator
1.Extended range: 120°-180° stroke offers precise control.
2.Versatility: Ideal for multi-position applications.
3.Flow control: Larger stroke ensures precise fluid adjustment.
4.Durability: Robust design ensures reliability.
5.Energy efficiency: Air-powered, reduces energy consumption.
6.Safety: Inherently safe in hazardous environments.
7.Easy maintenance: Simple design minimizes downtime.
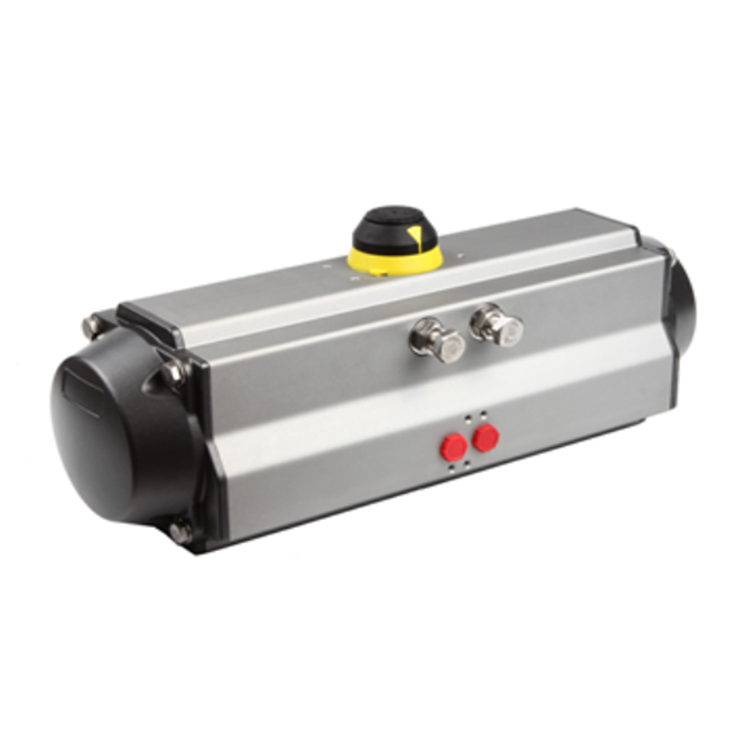
120°-180° Stroke Pneumatic Actuator Gallery
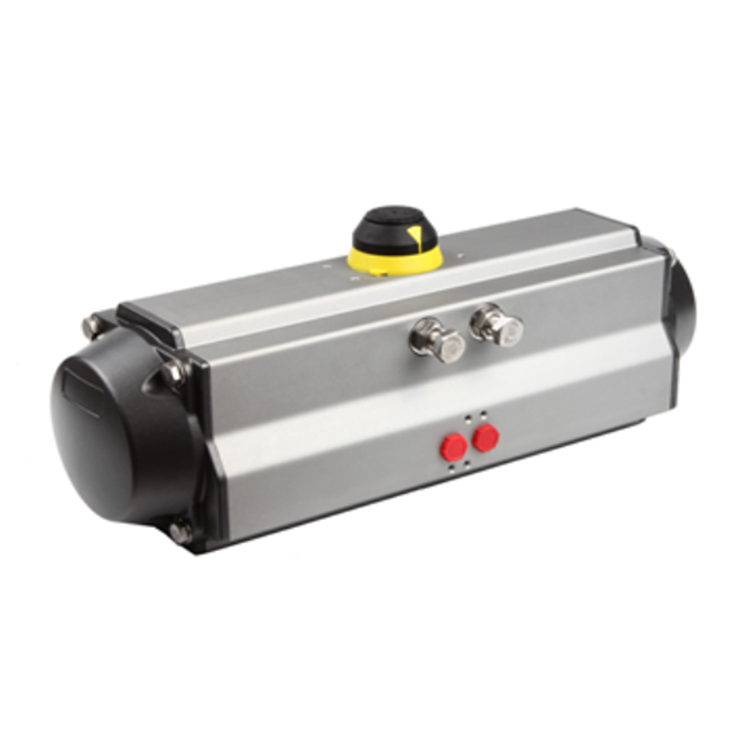
120°-180° Stroke Pneumatic Actuator
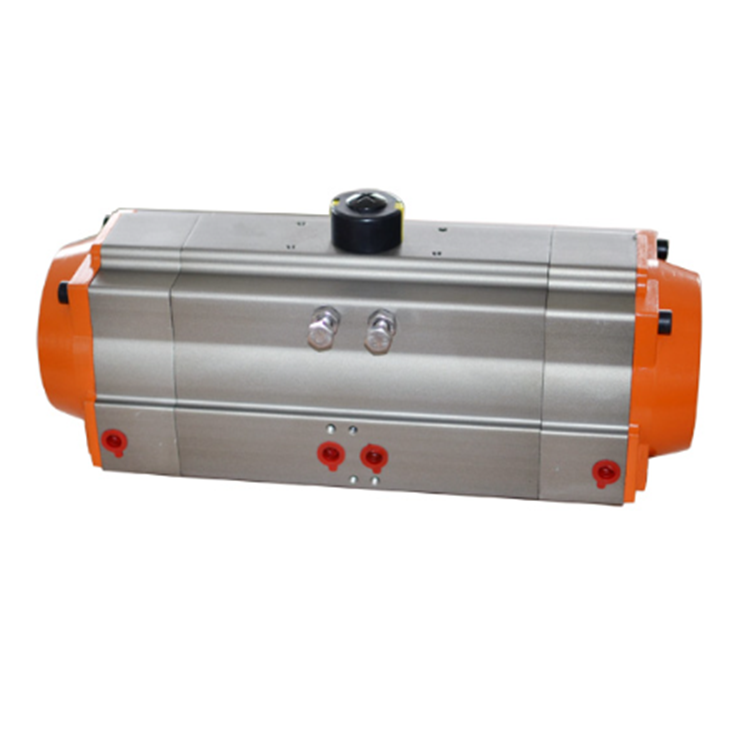
120°-180° Stroke Pneumatic Actuator
Every LORZEN 120°-180° Stroke Pneumatic Actuator has gone through highly controlled conditions to ensure the high quality of your Pneumatic Actuators.
The advantages of a 120°-180° Stroke Pneumatic Actuator include:
1.Extended Range of Motion: The primary advantage of a 120°-180° stroke is the extended range of motion compared to standard 90° actuators. This allows for greater control over the equipment it’s attached to, such as valves or dampers, which can be beneficial in applications that require more than just the typical open/close functionality.
2.Increased Versatility: The extended stroke allows the actuator to be used in a wider range of applications. It could be used in applications where the controlled device needs to be in more than two positions.
3.Better Flow Control: In the case of valve control, a larger stroke can provide better control over the flow of fluid. It can allow for more precise adjustments, leading to improved process control.
4.Enhanced Durability: Like other pneumatic actuators, a 120°-180° stroke actuator is typically robust and durable, capable of operating in harsh environments.
5.Energy Efficiency: Pneumatic actuators use air, a readily available and renewable resource, as their power source. They don’t require electricity or hydraulic fluid, reducing energy consumption and environmental impact.
6.Safety: Pneumatic actuators are inherently safe to use in hazardous environments where electrical devices might pose a risk of sparking and causing an explosion.
7.Ease of Maintenance: Pneumatic actuators are generally easier to maintain than their electric or hydraulic counterparts due to their simpler design and fewer moving parts.
Remember, the specific advantages can depend on the design of the actuator and the application it is used in. Always consult with the manufacturer or a knowledgeable engineer to understand the best choice for your specific needs.
The product features of a 120°-180° Stroke Pneumatic Actuator can vary depending on the specific model and manufacturer, but generally, they include the following:
1.Extended Stroke: The defining feature is the extended stroke, typically ranging from 120° to 180°. This allows for greater control of the actuator and the ability to handle more complex tasks than standard 90° actuators.
2.Robust Construction: These actuators are usually built to be robust and durable, capable of withstanding harsh operating conditions and high loads.
3.Precision Control: They often offer precise control over the position of the actuator, making them suitable for applications that require accurate and repeatable positioning.
4.Versatility: These actuators can be used in a wide range of applications, thanks to their extended stroke and precise control capabilities.
5.Safety Features: As with other pneumatic actuators, these devices are inherently safe to use in potentially hazardous environments due to their use of air pressure as a power source.
6.Energy Efficiency: They are typically energy-efficient, using compressed air as a power source instead of electricity or hydraulic fluid.
7.Ease of Maintenance: Their design often allows for easy maintenance, with fewer moving parts than other types of actuators.
8.Compatibility: Many 120°-180° stroke pneumatic actuators are designed to be compatible with a variety of control systems and mechanical devices.
9.Customizability: Depending on the manufacturer, these actuators may be customizable to better fit the specific requirements of different applications.
10.Fast Response Time: Pneumatic actuators generally have a quick response time, making them suitable for applications that require rapid action.
As always, the specific features can depend on the particular model and manufacturer, so it’s important to consult the product specifications or speak with a representative from the manufacturer to understand the exact features of a given product.
Product characteristics:
Product characteristics:The product characteristics of a 120°-180° Stroke Pneumatic Actuator can vary depending on the specific model and manufacturer, but generally, they can include:
1.Stroke Length: The key characteristic is the extended operational stroke, typically ranging from 120° to 180°. This gives the actuator a wider range of control and makes it suitable for more complex tasks.
2.Material: The actuator is often made from durable materials like stainless steel, aluminum, or other alloys to withstand harsh operating conditions and high pressures.
3.Operating Pressure: These actuators can typically operate under a wide range of air pressures, depending on the requirements of the specific application.
4.Torque Output: The torque output can vary greatly depending on the size and design of the actuator, but it is generally high enough to control a range of industrial equipment.
5.Temperature Range: These actuators are usually designed to operate in a wide range of temperatures, making them suitable for various industrial environments.
6.Size and Weight: The size and weight of the actuator can vary depending on the specific model, but they are generally compact and lightweight relative to their power output.
7.Connection Type: The actuator will have a specific type of connection for attaching to the equipment it is controlling, such as flange or threaded connections.
8.Control Type: These actuators can typically be controlled by a variety of methods, including manual control, remote control, and automated control systems.
9.Sealing: Good sealing is often a key characteristic, ensuring that the actuator operates efficiently and reliably, and minimizing the risk of leaks.
10.Speed of Operation: The speed at which the actuator can move between positions can be an important characteristic, especially in applications that require rapid response times.
As always, these are general characteristics and can vary depending on the specific model and manufacturer. It’s important to refer to the product specifications or consult with the manufacturer to understand the exact characteristics of a specific actuator.
Operating Parameters:
Output torque:8 N.m – 10000 N.m
Structure:Rack and pinion structure
Application:Ball valve, butterfly valve, plug valve and other valv
Air Supply Pressure:3 – 8 bar
Cylinder body material:Aluminum alloy (surface coating: hard anodized)
End cover material:Die-casting aluminum alloy (surface coating: powder spraying)
Air source control:Through filtered compressed air, no need lubricate oil,the oil must suit for NBR under lubricated condition.
Applicable ambient temperature:Standard -20℃~80℃
Low temperature -40℃~80℃
High temperature -15℃~120℃
Flange standard:ISO 5211 / DIN3337
Rotate stroke:0 – 180°(+/-5°)
Service life:Maintenance-free and low friction , switch service life more than 1 million times.
Performance Testing
Our state-of-the-art facilities allow rigorous testing to validate function, endurance and environmental protection.
Quality Assurance
100% testing and inspection ensures superior performance of every actuator.
LORZEN Pneumatic Actuators Are Utilized Across Various Sectors, Including:





Actuator Design
120°-180° Stroke Pneumatic Actuator Search
Pneumatic control system is an important part of any valve and actuator. has rich experience in gas circuit control to meet clients’requirements for on-off, regulating and urgent switching-off. Gas circuit system can be installed on a panel or in control cabinet, or in-stalled on an actuator or placed separately.
- +8613736966003
- sales@lorzval.com
- Lorzen Factory Park, Linyang Industrial District, Oubei Town, Yongjia County, Wenzhou City, Zhejiang Province, China
120°-180° Stroke Pneumatic Actuator Related Information
Installation and Maintenance
Installation and Maintenance
The installation and maintenance of a Fork Pneumatic Actuator are relatively straightforward. Here are some basic steps:
Installation: During the installation process, it’s important to ensure the actuator is correctly aligned and secured in the right position. The actuator should be properly interfaced with the driven device (such as a valve or other mechanical component) to ensure accurate and efficient operation.
Maintenance: Maintenance of the actuator typically involves regular inspections and replacement of worn parts. This might include replacing seals, cleaning and lubricating moving parts, and checking and adjusting the control system. In most cases, just carrying out these maintenance steps periodically can ensure long-term reliable operation of the actuator.
Industry Applications/Functional Uses
Industry Applications/Functional Uses
Fork Pneumatic Actuators have a wide range of uses in many different industries and applications. Here are some of the main application areas:
Manufacturing: On automated production lines, these actuators can be used to control a variety of mechanical equipment such as valves, drums, conveyors, etc.
Energy Sector: In the oil, gas, and electricity industries, these actuators can be used to control various types of valves, ensuring efficient distribution and use of energy.
Chemical Industry: In chemical processes, these actuators can be used to precisely control conditions for various chemical reactions, such as temperature, pressure, and flow rate.
Water Treatment: In water treatment facilities, these actuators can be used to control various equipment like pumps, valves, and filters, ensuring effective water treatment.
Food and Beverage Industry: In the production process of food and beverages, these actuators can be used to control various equipment like mixers, ovens, and packaging machines, ensuring efficiency and quality in the production process.
These are just some of the main application areas for Single Acting Fork Pneumatic Actuators. Thanks to their simple design and operating principle, these actuators can adapt to a variety of different applications and environments.